OptiGrader CRC
-optimization solution for slicing wood
OptiGrader CRC optimization solution for slicing lumber in remanufacturing
The key question in lumber remanufacturing is how to cut and slice optimum pieces from the boards for various purposes.
The task is extremely demanding since some of the material is easily wasted or used for secondary purposes, even when dealing with first class raw materials.
For example, wane may be left on clear lumber that is cut from butt log during the edging phase. This means that remanufacturing receives a higher volume of clear lumber material which would otherwise end up being chipped.
Maximizing quality through active slicing control
The OptiGrader CRC (Cross-cut, Rip-saw, Cross-cut) system uses a machine vision application based on neurocomputing to identify the board grade factors, such as knots and other defects, and combines them with the end products’ market pricing. With these factors as the basis, the OptiGrader CRC maximizes the amount of money receivable for the raw materials and computes an optimal board slicing method for several remanufacturing purposes.
The system combines the measurements and optimization by means of a single device controlling all the phases of cutting and slicing: cross-cutting, rip-sawing and cross-cutting. Compared to a conventional cutting and ripping line, the benefit is that there is no need for three separate optical scanners to control the different processes.
Intelligent cutting and ripping maximizes the recovery of raw material of the highest value. This can increase the end product value by as much as 30 percent while providing a huge boost to the profit.

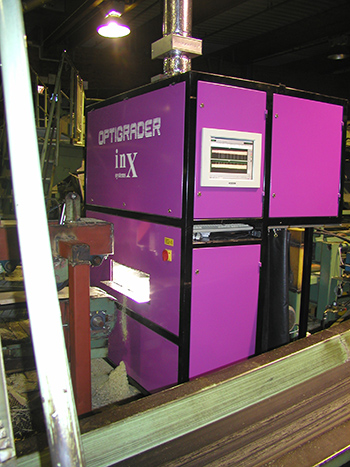
An award-winning machine vision application
The OptiGrader CRC examines the board or blanket from 1 to 4 directions as required. A matrix camera is used to measure the dimensions (1,000 images per second) and a true-color line-scan camera is used to measure the grade properties (4,000 images per second). The system identifies the grade factors with the aid of a machine vision application based on neurocomputing that simulates human brain activity. The system can be taught to identify new defect types with the aid of concrete images.
The application has been awarded the EC Vision Prize for the best cognitive machine vision system, which reflects Inx-Services’ leadership in the development of self-learning measuring systems.
The image processing technology used by the system is patented.
Office electronics is no match for this line of work
The system electronics was designed for industrial conditions and the equipment processing power was dimensioned for machine vision applications that require massive computing power. This ensures the equipment reliability and the measurement accuracy, which cannot be achieved by computers that are designed for office purposes.
The user interface complies with the specific needs of wood processing, providing a clear view of the production in progress. The user sees the measurement results of all pieces being processed, and the required procedures computed by the optimizing system in a clear graphic form.
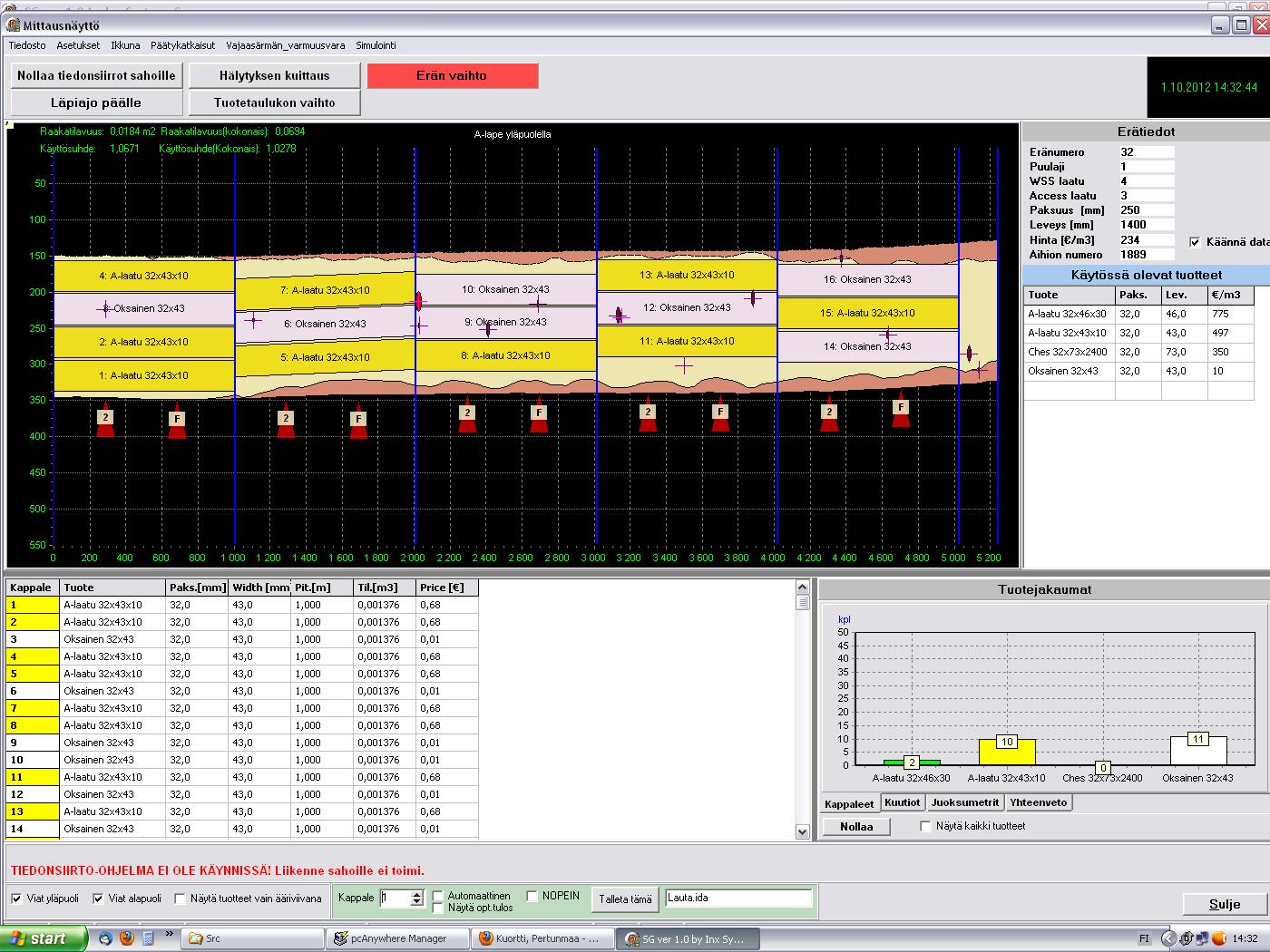