ScanLog 3D
-profile log scanner
ScanLog 3D measuring solution for log profiling
Up until now, log sorting has been based on the top diameter. This has also meant that a number of minor natural anomalies such as sweep, taper and ovality have been somewhat ignored.
The new-generation ScanLog 3D log profile measuring system changes this situation. The system identifies the actual log form and, if accompanied with the OptiLog software, enables sorting based on the saw pattern, instead of top diameter. Provided that the saw patterns can be controlled in real time, OptiLog can optimize the saw pattern for each individual log.
Both methods increase the yield significantly and boost the profit, even by several million euros per annum.
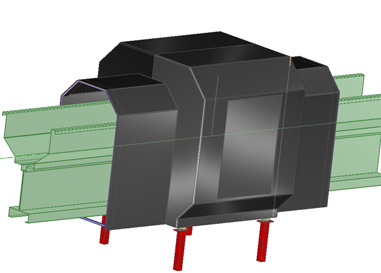
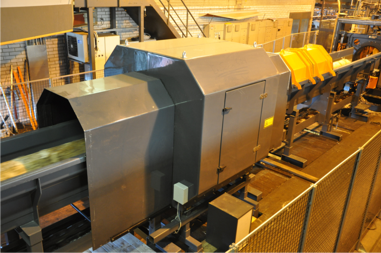
Saw-pattern-based sorting improves the yield and quality
ScanLog 3D measures the log form, volume, diameter, length, sweep, taper and ovality. The OptiLog software uses this data to compute the most profitable saw pattern for each log and controls log sorting accordingly. In saw-pattern-based sorting, the system matches the log profile measured to the categories stored in the pattern library and directs the log into the selected slot.
The ScanLog 3D measurement results are used on the saw line to control log rotation and cant curve sawing. In addition, the measurement results can be used by the OptiLog software at a later stage to re-calculate saw patterns and simulate the sawing process.
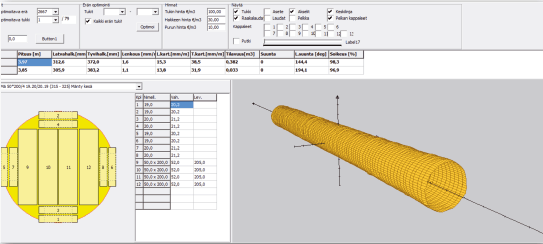
Measuring the bark-free diameter
A bark thickness measuring system is available for the log measuring equipment to eliminate the bark effect from the log profile. Consequently, you no longer need to guess the bark thickness for the log sorting phase. This allows a more rigorous definition of the sawing categories, which also improves the yield.
Fast and accurate measurements
ScanLog 3D identifies the log surface form with the aid of lasers and four intelligent matrix cameras. The system measures the log profile 200 times per second at a diameter resolution below one millimeter. The maximum range of a measurable diameter is 650 millimeters.
Office electronics is no match for this line of work
The system electronics was designed for industrial conditions and the equipment processing power was dimensioned for machine vision applications that require massive computing power. This ensures the equipment’s reliability and the measurement accuracy, which cannot be achieved by computers designed for office purposes.
The user interface complies with the specific needs of wood processing. It provides a clear view of the production in progress and shows the measurement results of each log in a clear form on the operator’s screen.